Nano impact testing – The quick way to analyze erosion behavior of thermal barrier coatings
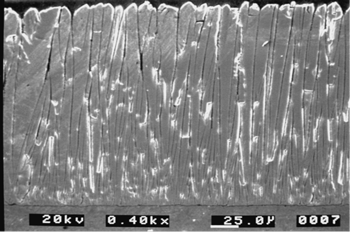
Fig. 1: SEM image of the columnar structure of a thermal barrier coating
Nano impact is a patented measurement option for the nano mechanical testing platform NanoTest Vantage.
Originally developed for material impact strength testing on the nano scale, this innovative measurement method is now mainly used in the development of wear protective coatings like diamond-like-carbon (DLC).
In a cooperation between the British universities of Birmingham and Cranfield and the Chinese Southeast University, nano impact tests were used to analyze the erosion behavior of 150 µm thick thermal barrier coatings (TBC) for airplane engines. Due to heat aging, the columnar microstructure of the coatings (Fig. 1) and their mechanical properties (see table) change. Nano impact tests allow higher dynamic strain rates and are thus better suited for this application than conventional nanoindentation tests. Its ability to analyze individual columns and column clusters is another advantage compared to conventional bulk erosion tests.
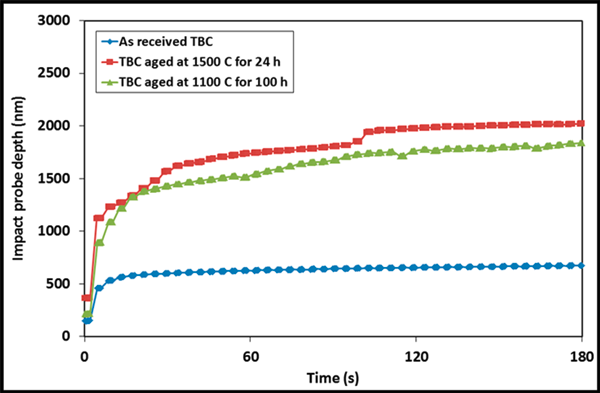
Fig. 2: Comparison of three analyzed TBC in a repetitive nano impact test at an impact rate of 0.25 Hz. Clearly visible is the dramatic impact depth increase on the thermally treated coatings within only seconds.
Single-impact tests showed that heat aging results in increased dynamic hardness and stiffness of the TBC. Repetitive nano impact tests showed a difference between the impact strength of heat treated and non-treated thermal barrier coatings (Fig. 2). Which means they showed a good correlation with common erosion tests. Presumably, thermal aging causes the TBC’s columnar microstructure to sinter. This means that cracks that occur after the impact propagate more easily through the column structure interfaces and that, in regards to volume, individual impacts remove more material.
Mechanical properties of investigated thermal barrier coatings
In this case, nanoindentation has proven unsuitable for the prediction of the erosion behavior of TBC.
Nano impact testing on the other hand showed a clear correlation with prior erosion tests and is a promising and quick alternative to predict erosion behavior.
Thermal barrier coating | Hardness [GPa] | Reduced modulus [GPa] |
---|---|---|
As received | 8.5 | 153 |
24 h @ 1500 °C Precipitated on ZrO2 | 15.1 | 157 |
100 h @ 1100 °C Precipitated on Al2 O3 | 16.9 | 190 |