AFSEM nano
Quantum Design AFSEM®nano AFM InsertAFSEM nano is an atomic force microscope (AFM), designed for integration in a SEM or Dualbeam (SEM/FIB) microscope. Its open access design allows you to simultaneously operate SEM and AFM inside the SEM vacuum chamber. The correlated image data of AFM and SEM enable unique characterization of your sample, and the combination of complementary techniques is a key success factor for gaining new insights into the micro and nano worlds.
AFSEM nano lets you simultaneously image your sample with high resolution, create true 3D-topography representations, and accurately measure heights, distances and even material properties, all while maintaining the large SEM field of view to position your AFSEM nano cantilever exactly where you want it. The powerful AFSEM nano control software allows for optimized and intuitive measuring, system handling, and data analysis.
- Small size; does not impede SEM operation
- Multiple measurement modes available
- Uses self-sensing cantilevers
- Powerful easy-to-use control software
- Compatible with most SEMs/FIBs
Weitere Informationen
The AFSEM nano is a fully functional atomic force microscope and therefore is capable of all normal measurement modes expected from a standard AFM. Contact mode, intermittent contact mode, non-contact, force-volume, and phase contrast mode are all available and the user can switch between them easily using the controller software. The advanced modes, namely Conductive AFM (C-AFM), Magnetic Force Microscopy (MFM) and Electrostatic Force Microscopy (EFM) are also available by using the functional probes. Kelvin Probe Force Microscopy (KPFM) and Scanning Thermal Microscopy (SThM) are currently under development.
AFSEM nano - Introduction Video
Measurement modes:
Standard AFM
In contact mode, the tip is in contact with the surface of the sample and follows the topography closely in the repulsive regime. For contact mode long and soft cantilevers with low force constants are used.
(Figures 1 and 2) AFSEM nano image of a polymer surface obtained in contact mode.
In intermittent contact mode, also called dynamic mode, the cantilever is oscillated near its resonance frequency. When the tip comes close to the surface, the interaction between the tip and the sample causes the amplitude of the oscillation to change. As the cantilever is scanning over the sample, the height is adjusted to maintain a set cantilever oscillation amplitude. An AFM image is therefore produced by imaging the force of the intermittent contacts of the tip with the surface.
AFSEM nano image of freestanding graphene membranes obtained in intermittent contact mode.
(Figure 1) Correlative SEM/AFM image of the graphene membranes.
(Figure 2) High-resolution AFM image of a single freestanding graphene membrane.
In non-contact mode, the tip of the cantilever does not contact the sample surface. The tip is oscillated only with a very small amplitude and is affected only by the long-range forces and therefore neither sample degradation nor tip degradation occur.
AFSEM nano image of silicon micro-pillar surface obtained in non-contact mode
(Figure 1) Correlative SEM/AFM image of the micro-pillar surface.
(Figure 2) High-resolution AFM image of the micro-pillar surface decorated with nano-wire network.
In force-volume mode, force measurements are combined with topographic imaging. Typical AFM images depict the topography of a surface by measuring the action of a feedback loop to maintain a constant tip/sample interaction as the tip is scanned across the surface. The force volume data set combines nearly simultaneously measured topographic and force information into a single data set allowing the microscopist to test for correlations between forces and surface features.
AFSEM nano image of bone sample with a partially dissolved implant obtained in force volume mode.
(Figure 1) AFM Topography image of the bone area and transition region, where the implant is partially dissolved.
(Figure 2) Force volume data of the same area.
(Figure 3) Overlay of topography and force volume data.
C-AFM
Conductive AFM mode (C-AFM) measures the conductive properties of the sample using a conductive tip. The conductive tips used by AFSEM nano are produced using Focused Electron Beam Induced Deposition (FEBID) and are made of pure Platinum, which ensures their high stability and longevity. There is no extra module needed for C-AFM measurements.
AFSEM nano C-AFM image of a gold electrode on a silicon substrate.
(Figure 1) SEM image of the region of interest displaying the gold electrode with a porous transition region at the edge of the electrode structure.
(Figure 2) AFM Topography image of the electrode structure.
(Figure 3) C-AFM image of the electrode structure that reveals the highly conducting gold electrode as well as the non-conducting silicon surface region.
MFM
Magnetic AFM Mode (MFM) is used to study the magnetic properties of magnetic materials using a magnetic tip. The conductive tips used by AFSEM nano are produced using Focused Electron Beam Induced Deposition (FEBID) and are made of Fe/Co. AFSEM nano uses a dual pass technique: A first scan images the topography. Then a second scan, where the tip follows the measured topography with a set distance above the sample, measures the phase shift due to magnetic force between tip and sample. By default, the AFSEM nano is capable of this so called "lift-mode".
AFSEM nano MFM image obtained on a multilayered magnetic sample.
(Figure 1) AFM Topography.
(Figure 2) MFM Phase contrast revealing the different magnetic domains.
(Figure 3) Overlay of topography and magnetic signal.
Spezifikationen
AFSEM nano is the smallest AFM insert for your SEM/FIB. Its small size and weight enable easy integration in extremely space-limited environments. The full grade V titanium body offers optimized mechanical stability and performance.
Scanner |
|
AFSEM®nano scanner dimensions: | L/W/H = 61 mm x 61 mm x 28 mm |
Scanner weight: | 125 g |
Scan range: | x/y: 22 μm x 22 μm (closed loop) |
HV compatibility: | 1 x 10-7 mbar |
Scan mode: | AC-mode, Contact mode, C-AFM, |
Positioning Stage |
|
Travel distance: | x = 12 mm |
Coarse resolution: | x/y/z: step size 100 nm |
High-Speed Controller |
|
Input: | 6 channels (200 kHz, 24 bit, with predefined functions) |
Output: | 7 channels (200 kHz, 24 bit, with predefined functions) |
High voltage amplifier: | 3 high-bandwidth channels (x, y: 10 kHz, z: >400 kHz) |
Fast feedback loop: | 16 bit ADC > 500 MHz sampling rate, 20 bit DAC with < 1 μs settling time |
Closed loop operation |
|
3-axes coarse positioning control |
|
High-end support PC with PCIe lock-in card |
|
PCIe card specifications: | 4 channels dual phase lock-in amplifier Sampling rate: >500 MS/s |
Monitor Outputs for All Sensor Signals |
|
Operating System Specifications and Features |
|
Software: | SXM control and imaging software. |
Q-control for fast scanning, especially in vacuum. | |
Scanner positioning stage control. | |
Proprietary data analysis software included. | |
File formats fully compatible with Gwyddion and SPIP. | |
Windows 11/64 bit operating system included. |
Downloads
Videos
Kontakt
+49 6157 80710-12 | |
+49 6157 80710912 | |
E-Mail schreiben |
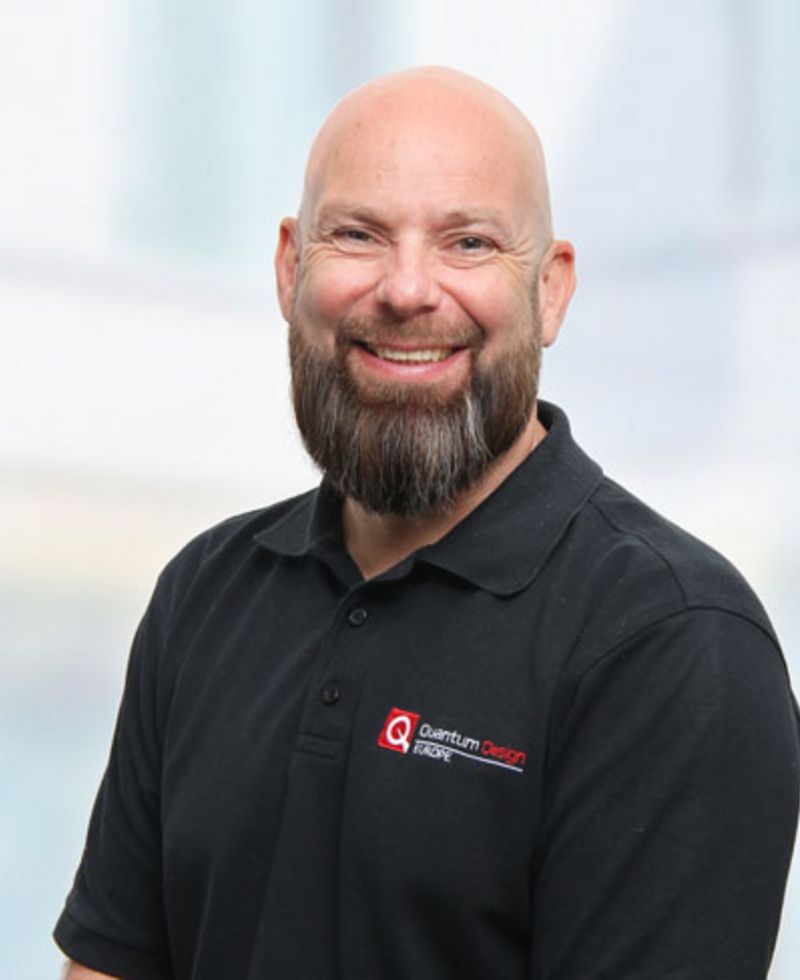
+49 6157 80710-841 | |
E-Mail schreiben |
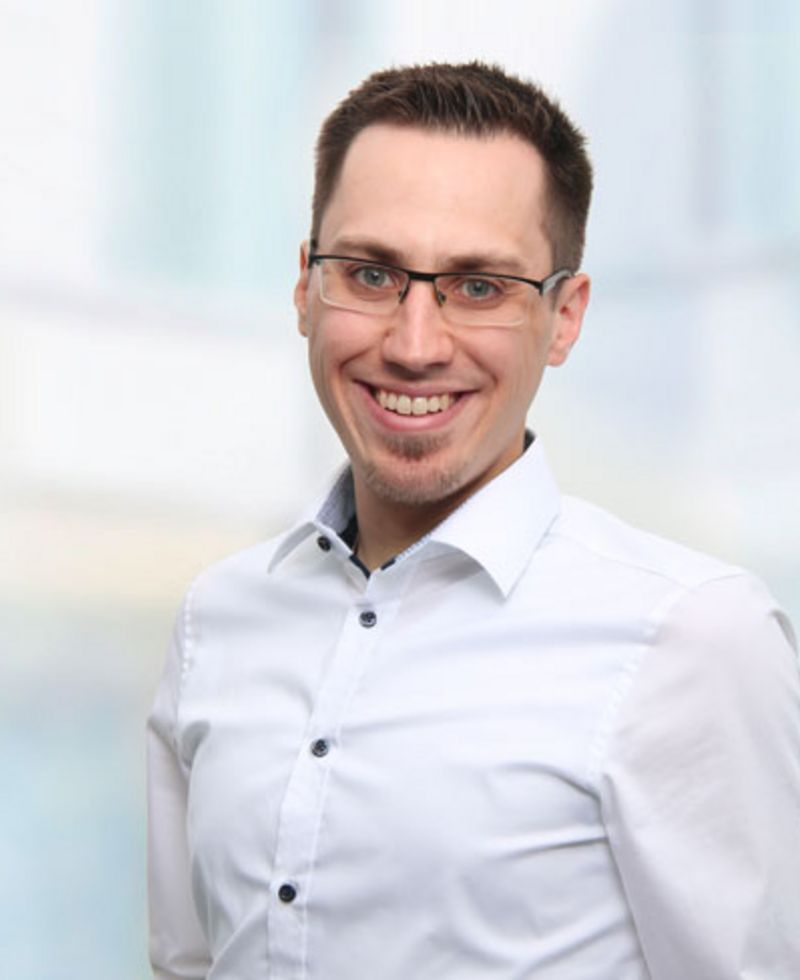