UV-curing applications: Understanding the specifications of light measurement devices – Part 2
Integrated irradiance as critical size
In UV-curing processes, the following physical units are used to compare the respective applications and measurements: Irradiance is given in W/cm² and dosage is given in J/cm². It is important that the UV measurement device can fulfill both the minimal and maximum requirements for irradiance and dosage.
Irradiance is the amount of light that hits a surface. It is also referred to as the intensity of the UV light. A higher UV-intensity is often necessary with
thicker substrates so it can penetrate deep enough to ensure proper curing. Longer UV-wavelengths penetrate deeper and are used whenever curing depth is important.
The dosage is the amount of irradiance over time. It is determined by W/cm² x seconds. It is also called integrated irradiance. The total UV-load during the curing process is a critical size for all lamp types, photo initiators and light measurement devices. It allows changes of the intensity on the conveyor belts and of the conveyance speed, alignment and distance.
Dosage measurement considers intensity fluctuations during measurement cycles and over long periods of time. This way it only takes one value to check if a process delivers enough total radiance. As the lamp intensity decreases with age, the operating lifetime can be extended by extending the dwell time. This prevents premature and expensive lamp changes.
Data analysis allows troubleshooting
Data storage and the comparison of measurements inside the UV radiometer can be of great use for troubleshooting light sources and the radiometer itself. When irradiance/dosage fall below a minimum value, the system must be serviced.
Temperature monitoring inside the measurement system is also a helpful feature as all sensors are subject to drift when warming up. By monitoring sensor temperatures, measurement mistakes can be avoided. Sometimes, a temperature that is too high can be an indicator that a substrate which should not be overheated has failed.
Profiling is a graphical display of the irradiance over time. It is particularly helpful for troubleshooting multi-lamp systems, because it allows recognizing problems of individual lamp or reflector setups. Without profiling, a measurement system would have to be placed underneath each individual lamp. Profiling is a fast and simple method to visually monitor the stability of the sources through time, determine the best warm-up phase and to troubleshoot.
Some systems not only store a base line but also allow data analysis. This may include a comparison of the stored baseline with the current measurement. Measurement data is stored internally and can be exported to a spreadsheet.
The new CureRight series ILT800 comprises data storage, temperature and profile creation.
Contact
+49 6157 80710-15 | |
+49 6157 80710915 | |
Write e-mail |
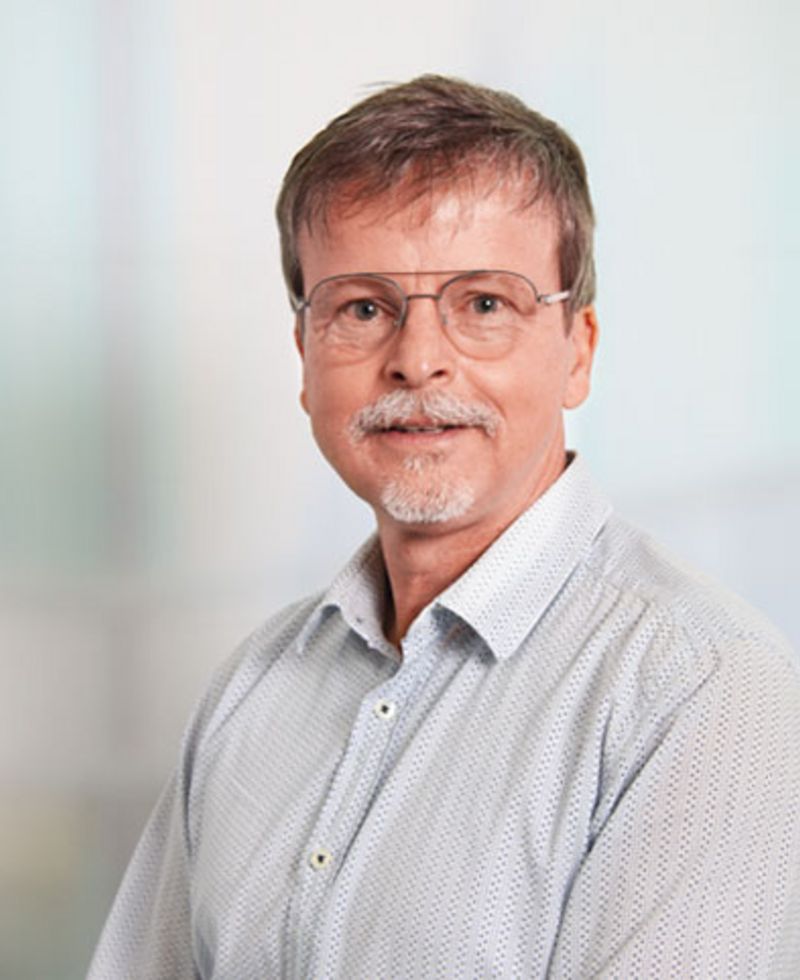