Cryogenic temperature controllers
From Lake Shore CryotronicsTemperature controllers for cryogenic applications are based on closed loop PID control. Also often called feedback control. With the help of this feature the temperature controllers from Lake Shore Cryotronics cover a low temperature down to 100mK and up to 1.500K. The control loops feature up to 100W heater power output. In the feedback control mode, the controller attempts to keep the load at exactly the user entered setpoint, which can be entered in sensor units or temperature. To do this, it uses feedback from the control sensor to calculate and actively adjust the control (heater) output. The control algorithm used is called PID.
Easy product selection for quick inquiries
Takes you to our "Lake Shore Inquiry System" where you can select the sensors, monitors and controllers you need and get an immediate response.
- 100mK to 1.500 K temperature range
- Up to 4 PID-controlled outputs with up to 100W
- Wide range of supported temperature sensors
- Ethernet, USB and IEEE-488 interfaces
Further information
More Information about each model:
Closed loop PID control
The PID control equation has three variable terms: proportional (P), integral (I), and derivative (D). The PID equation is:
where the error (e) is defined as: e = Setpoint – Feedback Reading.
The proportional term, also called gain, must have a value greater than zero for the control loop to operate. The value of the proportional term is multiplied by the error (e) to generate the proportional contribution to the output: Output (P) = Pe. If proportional is acting alone, with no integral, there must always be an error, or the output will go to zero. A great deal must be known about the load, sensor, and controller to compute a proportional setting (P). Most often, the proportional setting is determined by trial and error. The proportional setting is part of the overall control loop gain, as well as the heater range and cooling power. The proportional setting will also need to change if either of these changes.
In the control loop, the integral term, also called reset, looks at error over time to build the integral contribution to the output:
By adding integral to the proportional contribution, the error that is necessary in a proportional-only system can be eliminated. When the error is at zero, controlling at the setpoint, the output is held constant by the integral contribution. The integral setting (I) is more predictable than the proportional setting. It is related to the dominant time constant of the load. Measuring this time constant allows a reasonable calculation of the integral setting.
The derivative term, also called rate, acts on the change in error with time to make its contribution to the output:
By reacting to a fast-changing error signal, the derivative can work to boost the output when the setpoint changes quickly, reducing the time it takes for temperature to reach the setpoint. It can also see the error decreasing rapidly when the temperature nears the setpoint and reduce the output for less overshoot. The derivative term can be useful in fast changing systems, but it is often turned off during steady state control because it reacts too strongly to small disturbances or noise. The derivative setting (D) is related to the dominant time constant of the load.
Manual output
Manual output can be used for open loop control, meaning feedback is ignored and the heater output stays at the user’s manual setting. This is a good way to put constant heating power into a load when needed. The manual output term can also be added to the PID output. It is possible to set an output value close the one needed and let the controller do the fine tuning to reach the set point.
NOTE: Manual output should be set to 0 when not in use.
Specifications
Model 325 Cryogenic Temperature Controller
- Operates down to 1.2 K
- Two sensor inputs
- Supports diode, RTD, and thermocouple sensors
- Sensor excitation current reversal eliminates thermal EMF errors for resistance sensors
- Two autotuning control loops: 25 W and 2 W maximum
- Control loop 2: variable DC voltage source from 0 to 10 V maximum
- IEEE-488 and RS-232C interfaces
Model 335 Cryogenic Temperature Controller
- Operates down to 300 mK
- Two configurable PID control loops providing 50 W and 25 W or 75 W and 1 W
- Autotuning automatically collects PID parameters
- USB and IEEE-488 interfaces
- Supports diode, RTD, and thermocouple temperature sensors
- Sensor excitation current reversal eliminates thermal EMF errors for resistance sensors
Model 336 Cryogenic Temperature Controller
- Operates down to 300 mK
- Two PID control loops: 100 W and 50 W into a 50 or 25 Ω load
- Autotuning automatically collects PID parameters
- Ethernet, USB and IEEE-488 interfaces
- Supports diode, RTD, and thermocouple temperature sensors
- Sensor excitation current reversal eliminates thermal EMF errors for resistance sensors
Model 346 Cryogenic Temperature Controller
- Operates down to 300 mK
- 10 sensor inputs, optionally up to 26
- Supports diode, RTD, and thermocouple sensors
- 8 heater outputs with 4 pcs a 100 W and 4 pcs a 1 W
- Broken lead detection
- USB, Ethernet and optional GPIB interfaces
Model 350 Cryogenic Temperature Controller
- Ideal for use with He-3 systems and other ultra-low temperature refrigeration platforms
- Down to 100 mK
- Optimized performance with Cernox® RTDs
- Minimal self-heating
- High resolution measurement
- 4 independent control loops and a broad range of I/O configurations
- 4 PID-controlled outputs: 75 W warm-up heater, 1 W sample heater, and 2 auxiliary 1 W ±10 V outputs
Model 372 AC Resistance Bridge
- Temperature measurement and control capabilities for dilution refrigerators (DRs)
- Temperature control below 100mK
- Patented noise rejection technology*
- AC measurement signals
- Low noise signal recovery
*U.S. Patent #6, 501, 255, Dec., 2002, "Differential current source with active common mode reduction," Lake Shore Cryotronics, Inc.
Downloads
Videos
Contact
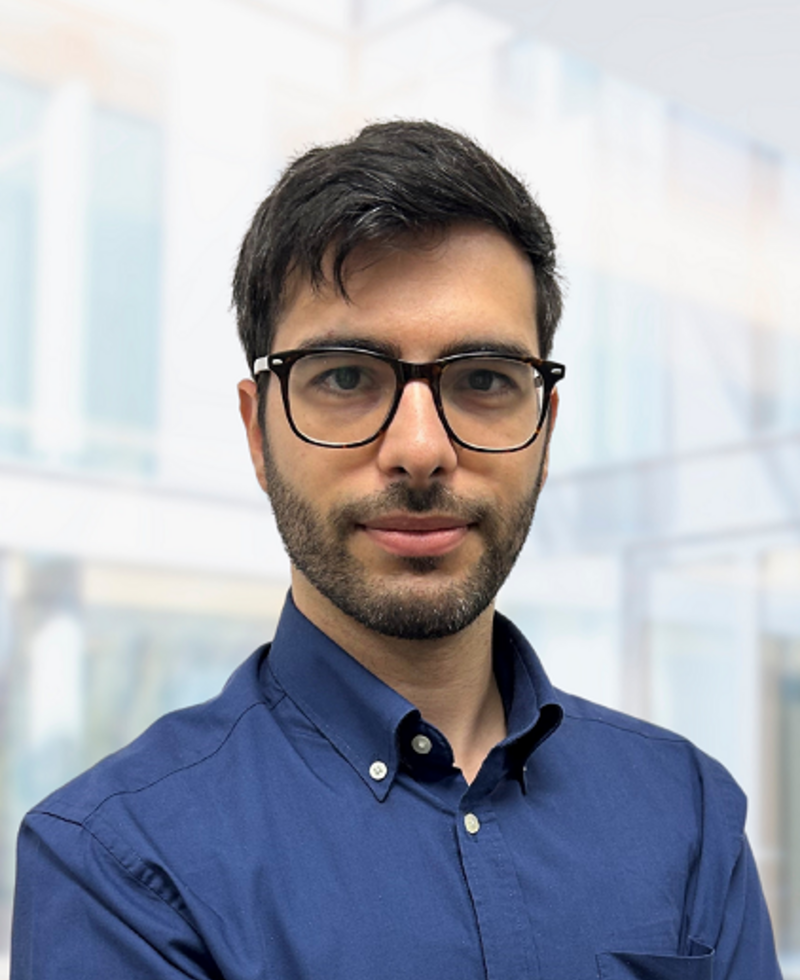